After two years of construction, SAMSON has opened the ROLF SANDVOSS INNOVATION CENTER – the most modern R&D and test center for valve engineering – on the eastern end of its Frankfurt site. The new, integrated R&D and test center enables all companies within the SAMSON group to meet the future requirements for testing and R&D activities. At the same time, the facilities of the ROLF SANDVOSS INNOVATION CENTER are open to SAMSON's customers and partners for research and certification so that the center can be run at a profit.
An area of more than 7000 m² is available for prototyping, simulations and a wide variety of tests. New fields in valve R&D, for example data analysis and cloud technologies, are being explored in the ROLF SANDVOSS INNOVATION CENTER in addition to the traditional research topics, such as materials science, flow engineering, cryogenics, acoustics, control engineering, device safety and system integration.
Work in the ROLF SANDVOSS INNOVATION CENTER is focused on the digital transformation of SAMSON products. Important foundations for this have been laid by equipping the center with complex plant engineering and a sophisticated digital infrastructure. They enable SAMSON to cover a wide variety of tests, process media, process conditions and fields of application. At the same time, they constitute the ideal base for the research, development and testing of SAMSON products for all Internet of Things and Industry 4.0 environments.
The entire infrastructure, which includes more than 200 test instruments, enables SAMSON to quickly develop new prime-quality products. These products achieve a high level of reliability in a wide variety of applications already when they are launched onto the market.
Virtual tour
This tour version is not available in Microsoft® Internet Explorer. If you are using Internet Explorer, please click here
Prototype construction
Prototype construction plays an important role in product development. It provides essential information for implementation in series production, particularly when designing complex parts. In addition, prototyping focuses on future manufacturing methods.
In the ROLF SANDVOSS INNOVATION CENTER, traditional tools machinery as well as CNC machining centers are used for prototype construction. Additive manufacturing of plastic parts based on 3-D design data is already possible. Implementing additive manufacturing also for metal and ceramic materials is planned.
Materials engineering
Using suitable materials is key to achieve durable, reliable products. As a result, one of the main tasks of materials science and engineering is to assess materials and parts to determine their maximum permissible conditions of use.
As products are not always installed in moderate environments, the ROLF SANDVOSS INNOVATION CENTER provides facilities to simulate the different atmospheric conditions that exist across the world. Accelerated simulations help determine the resistance of metal and non-metal parts as well as entire devices to these conditions. The processes involve exposing the parts to seawater and industrial atmospheres, humid environments as well as different weather conditions.
Digital infrastructure
More than 200 test instruments are operated in the ROLF SANDVOSS INNOVATION CENTER based on a fully integrated measuring and automation system. Thanks to the digital infrastructure, it will be possible to perform real-time tests including simulations of various plant and operating conditions as well as compile and analyze the collected data. A modular communication infrastructure helps ensure that the smart SAMSON products are compatible with all common process control, engineering and asset management systems and that they can be connected to cloud computing systems. With this setup, research and development into shifting smart features to the field devices to achieve decentralized control can be intensified.
EMC and device safety
The electromagnetic compatibility and safety of SAMSON products is verified in the CE Lab.
Tests at frequencies up to 18 GHz can be performed in an anechoic chamber for radiated interferences and emission measurements. Stations to test electrostatic energy and conducted interferences, like they occur when the voltage drops or lightning strikes, also exist.
The tests completed in the CE Lab enable SAMSON to document the required CE compliance of our products.
Life cycle tests
SAMSON products are characterized by their long service life, even if they are operated in the most adverse process and ambient conditions. To achieve this durability, individual parts as well as complete control valves are subjected to life cycle tests in the ROLF SANDVOSS INNOVATION CENTER.
The tests cover the specimens‘ chemical, thermal and mechanical resistance as well as their flow characteristics and suitability for specific climate conditions. The available test facilities include various simulation and climatic cabinets, ovens and flow test benches.
Fluid mechanics
We are SMART IN FLOW CONTROL. We want to understand and control the flow of media. Process media in all possible conditions, such as liquids, gases, vapors, multi-phase flows and even liquids containing solid particles, can be simulated on different test benches in the ROLF SANDVOSS INNOVATION CENTER.
In the Flow Labs, valves in sizes up to DN 500 (optionally up to DN 1000) can be subjected to flow, acoustic and functional tests, they can be calibrated and their operation under specific plant conditions can be simulated.
Plant engineering
The complex plant engineering equipment and systems are at the heart of the ROLF SANDVOSS INNOVATION CENTER. They enable SAMSON to cover a wide variety of tests, process media, process conditions and fields of application.
Over two kilometers of pipes in nominal sizes up to DN 1000 are installed in the ROLF SANDVOSS INNOVATION CENTER. More than 250 valves in different sizes and pressure ratings manufactured by SAMSON and its subsidiaries are used to shut off and control the flow in the center‘s pipelines. An installed power of 5.5 MW serves to drive 18 pumps with different output pressures of up to 120 bar and flow rates as high as 9000 m³/h.
In the press
- CHEMICAL ENGINEERING: SAMSON OPENS NEW INNOVATION CENTER
- cpp - chemical plants & processes: Samson inaugurates valve development centre - Focus on process intelligence
- EuroHeat&Power: Samson Opens Test Center - Innovation Center Is Driving Digital Transformation
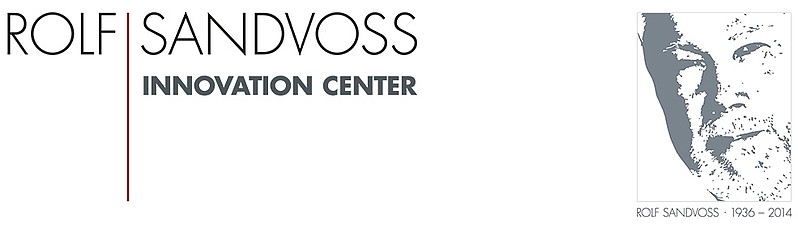
About Rolf Sandvoss
Rolf Sandvoss, great nephew of SAMSON's founding father, took over corporate responsibility for the Stuttgart company previously managed by his father at the early age of 24. In August 1965, Mr. Sandvoss was appointed to the SAMSON AKTIENGESELLSCHAFT Supervisory Board as one of the youngest members of the Sandvoss family. He quickly moved into the role as mediator and just eight years later, he became chairman of the Supervisory Board. In the following 28 years, he laid the foundations for SAMSON's evolution into a group of companies with worldwide operations, which currently employs 4,000 members of staff in over 40 countries. In 1962, Mr. Sandvoss also played a key role in the founding of the French subsidiary in Lyon and remained active on its executive board over many decades.
To honor his achievements, the Supervisory Board appointed him honorary chairman in September 2003. He continued his remarkable commitment to SAMSON in his role as honorary chairman until his death. His entrepreneurial spirit, reliable judgement and distinguished management style still influence the SAMSON corporate philosophy today. His commitment to the company and its workforce is exemplary of how the companies and staff work together at SAMSON.